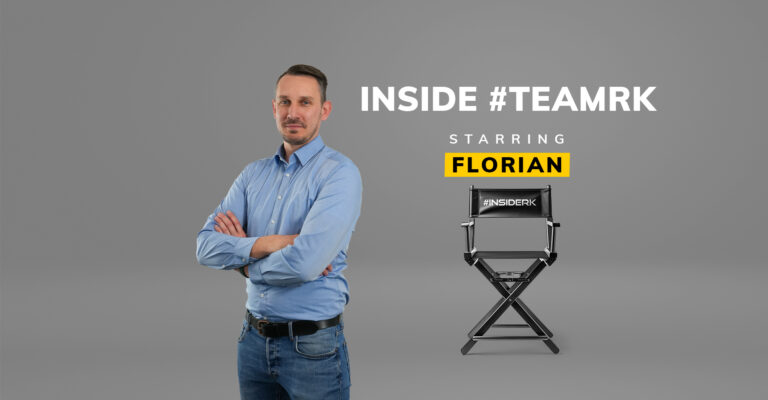
5.000 Teile
pro Tag
EINE PRODUKTIONSANLAGE
WIE EIN MASSANZUG
Die REINHOLD KELLER Group überzeugt mit Qualität sowohl in der Systemgastronomie, im Ladenbau, in der Hotellerie als auch bei der Ausstattung von Fitnessstudios. Nicht umsonst finden sich klingende Namen wie die zwei Fast Food Riesen McDonald´s und BURGER KING, Hotelketten wie Holiday Inn Express, Ibis, die bekannten Stores Superdry oder TK Maxx sowie die Marktführer im Fitnessbereich clever fit und McFit auf der Kundenliste.
INVESTITION IN DEN STANDORT – „MADE IN GERMANY“
Damit das auch so bleibt, investieren wir, die REINHOLD KELLER Group, konsequent in unsere Produktion, sowohl räumlich als auch technisch. Was uns von vielen anderen Unternehmen unterscheidet: Wir bauen konsequent eigene Ressourcen aus. Das heißt aus dem „Firmendeutsch“ übersetzt: Wir investieren in unsere Standorte – egal, ob es technologische Erweiterungen sind oder es um Mitarbeiter geht –, während viele Wettbewerber es sich zur Regel gemacht haben, so viel wie möglich ins Outsourcing zu übergeben. So machen wir es möglich, fast alle Innenausbaulösungen bei uns im Haus zu produzieren. Diese Produktionstiefe findet man nur noch ganz selten.
Bei uns erhält der Kunde Qualität „Made in Germany“ – was sie auch zu schätzen wissen, und das zum Teil seit vielen Jahrzehnten.
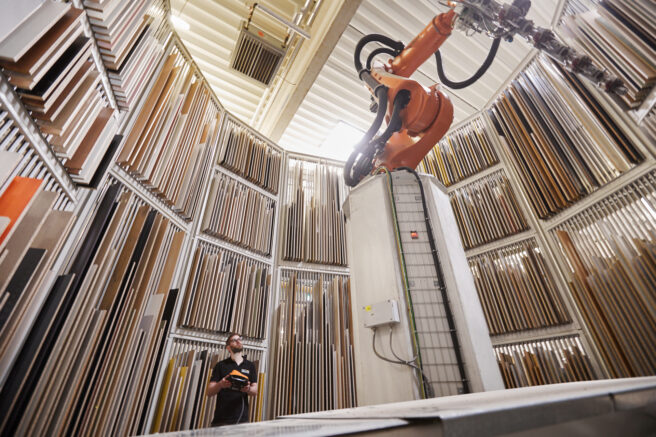
GROẞE BENEFITS FÜR DEN KUNDEN
Um diese Qualität unserem wachsenden Kundenstamm auch in Zukunft bieten zu können, und auf Anfragen noch flexibler und schneller reagieren zu können, haben wir gegen Mitte 2018 nach ca. 1,5jähriger Planung, Simulation sowie Umbau und Montage unsere neue teilautomatisierte Zuschnitt- und Bekantungsanlage angeworfen. Diese Investition in technischen Fortschritt ist für uns eine absolut logische Konsequenz gewesen, um unsere Kunden in Zukunft noch besser bedienen zu können. Größere Lagermöglichkeiten für unsere „Holzrohmaterialien“, generell höhere Kapazitäten in der Produktion sowie eine schnellere, reibungslosere und fehlerunanfälligere Abwicklung machen einen noch effektiveren und effizienteren Projektablauf möglich – ein klarer Benefit für den Kunden.
Die Ansteuerung des neuen Maschinenparks erfolgt derweil direkt aus unserer Arbeitsvorbereitung heraus. Soll heißen, das, was wir in 3D-Zeichnungen auf dem Rechner erstellen, wird vom Konstrukteur direkt auf die Maschine gegeben, ohne weitere Schnittstellen. Eben REINHOLD KELLER 4.0.
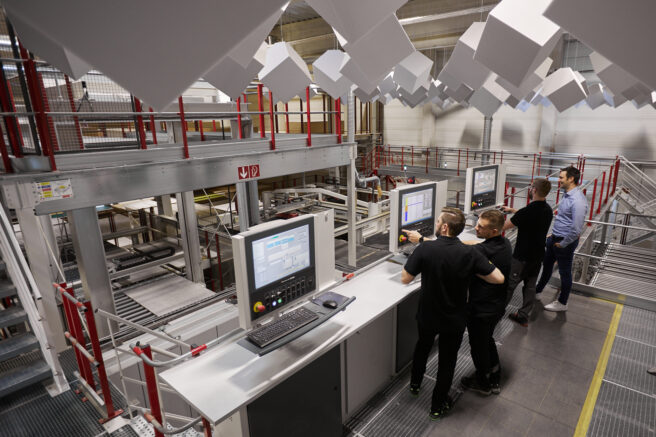
HOHE ANFORDERUNGEN
Als Partnerunternehmen für die Umsetzung dieser nicht gerade kleinen Aufgabe fiel die Wahl auf die IMA Schelling Group, dem Spezialisten für die Realisierung anspruchsvoller Anlagenlösungen für Holzbearbeiter.
Es ging uns nicht um eine „einfache“ Plattenzuschnittsanlage, vielmehr ging es um Schnittstellen-Minimierung durch direkte digitale Verknüpfungen zwischen einzelnen Prozessschritten. Kombiniert wurde das Ganze mit einer Fertigungsleittechnik – so ist jedes Teil zu jeder Zeit verfolgbar. Wir wissen nun somit, wann welches Teil zu dem entsprechenden Projekt wo ankommt, das Ganze natürlich prozessoptimiert und automatisiert.
Gleichzeitig war das Ziel die Lagerkapazität zu optimieren. In Kombination ergibt das dann eine merkliche Steigerung der Fertigungskapazität. Aber das war noch lange nicht alles an Ansprüchen, die wir an unsere neue Produktionsanlage stellten. Auch unser großes Teilespektrum sollte reibungslos auf der neuen Anlage laufen. So haben wir nun im 2Schicht-Betrieb eine Kapazität 5.000 (!) unterschiedliche Teile – also der Losgröße 1 – zu produzieren.
Daneben gab es auch noch andere „Kleinigkeiten“ zu berücksichtigen wie die räumlichen Grenzen. Die neue Anlage war in die bestehende Produktionshalle zu integrieren. Da gab es natürlich auch einige bauliche Gegebenheiten zu berücksichtigen. Die IMA Schelling Group nahm die Herausforderung an.
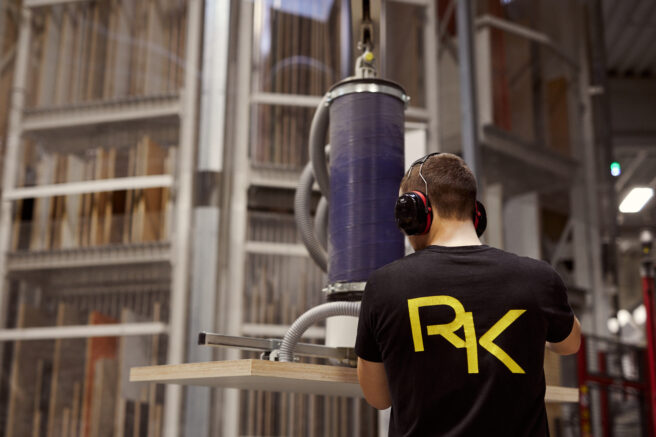
EINE PRODUKTIONSANLAGE WIE EIN MASSANZUG
Als Maßanzug für unseren Betrieb oder ähnlich könnte man die Produktionsanlage umschreiben, die unser Partnerunternehmen für uns konzipiert und umgesetzt hat. Das beginnt schon beim Lagerplatz. Dieser wurde zweistöckig angelegt, um die volle Kapazität auszunutzen, die unsere Halle bietet. Die gelieferten Platten werden nun, nachdem sie abgeladen wurden, eingescannt, auf den jeweiligen Lagerplatz eingelagert und bei Bedarf und je nach Projekt automatisch den Sägen zugeführt. Denn das System weiß, welches Material an welcher Stelle lagert.
Über drei Sägen werden die Platten auf die jeweiligen Maße anschließend zugeschnitten, bevor diese Teile dann über ein automatisches Transportsystem in ein sogenanntes Puffersystem zwischen Säge und Kantenanlage befördert werden. Auf diese Weise können Leistungsspitzen optimal ausgeglichen werden, und es kommt zu einer gleichmäßigen und sinnvollen Abarbeitung der Aufträge. Denn erst, wenn die nachgelagerte Kantenanleim-Maschine, die Combina, grünes Licht gibt, werden die Teile weitergeleitet. Die Kanten werden hochwertig bearbeitet – ein- bis vierseitig. Verleimt werden die Kanten mit PUR.
Verschnittreste werden übrigens für nachfolgende Aufträge eingelagert. Somit wird eine optimale Materialausnutzung gewährleistet. Wir gehen auch hier noch ein Stück weiter. Unsere Produktionsanlage ist so intelligent, dass sie bereits Reste von Teilen, die noch nicht einmal zugeschnitten wurden, für Folgeprojekte schon verplant. So vermeiden wir gleichzeitig noch eine unnötige Lagerung von Teilen.
Am Ende gelangt alles über eine Beschickungs- und Umsetzanlage zu entsprechenden Entnahmeplätzen. Das geschieht softwaregesteuert. Diese ist sogar in der Lage zu erkennen, ob die Teile weiterbearbeitet werden müssen. Hier ist auch der Treffpunkt mit allen anderen Komponenten für das jeweilige Bauteil, die nicht über die Anlage müssen – wie z.B. diverse Zukaufsteile. Alle Bauteile werden am Ende projektspezifisch zusammengeführt und durch unsere eigene Logistik an den jeweiligen Projektstandort geliefert.
GROẞE INVESTITION FÜR EINEN GROẞEN KUNDENNUTZEN
Dass nicht alles von Anfang an reibungslos läuft, ist wahrscheinlich jedem bekannt, der solch eine technologisch hochkomplexe Anlage mal zum Laufen gebracht hat. Das kostet vor allem intern noch einmal zusätzlich Kraft und Energie. Aber wir sehen auch, dass sich diese Investition absolut gelohnt hat und unseren Kunden vielerlei Mehrwerte in Zukunft bieten wird – höhere Flexibilität, geringere Fehleranfälligkeit, größere Genauigkeit, höhere Lagerkapazitäten, topp Qualität und eine schnellere Abwicklung.
Denn genau das ist unser täglicher Antrieb: dem Kunden den größtmöglichen Nutzen zu bieten, für den Kunden das bestmögliche Ergebnis zu erzielen.
Es tut sich noch einiges mehr rund um REINHOLD KELLER. Und wir möchten in Zukunft noch ein bisschen mehr hinter unsere Kulissen schauen. Unter #rkinside
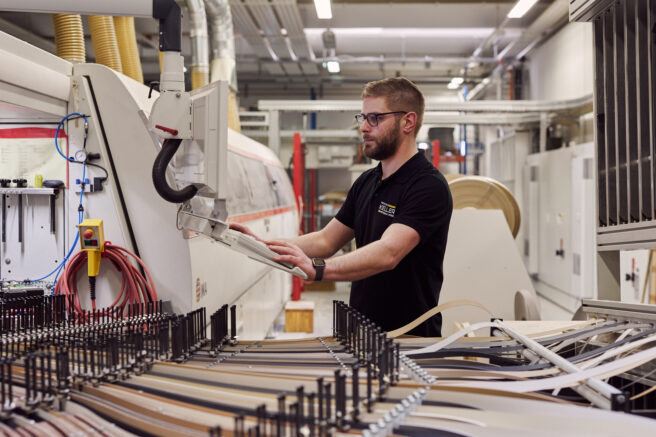
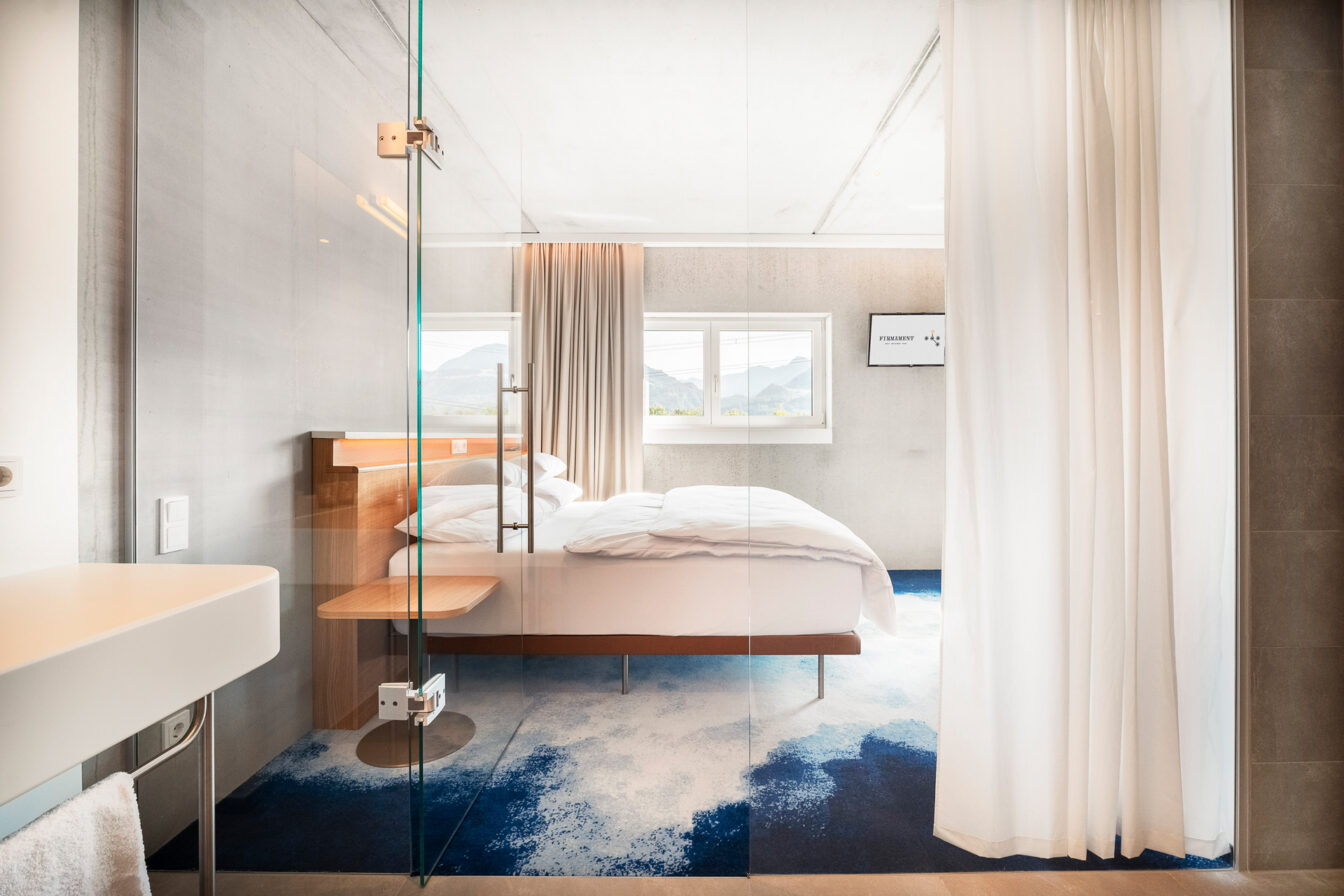